The SUB connector, also known as a Subminiature connector, is a type of electrical connector commonly used in various electronic devices and applications. These connectors are smaller in size compared to standard connectors, making them ideal for compact and space-constrained devices. The production process of SUB connectors involves several steps to ensure high quality and reliability. In this article, we will discuss the mainstream production process of SUB connectors in detail.
enter;margin:5px 0;'>
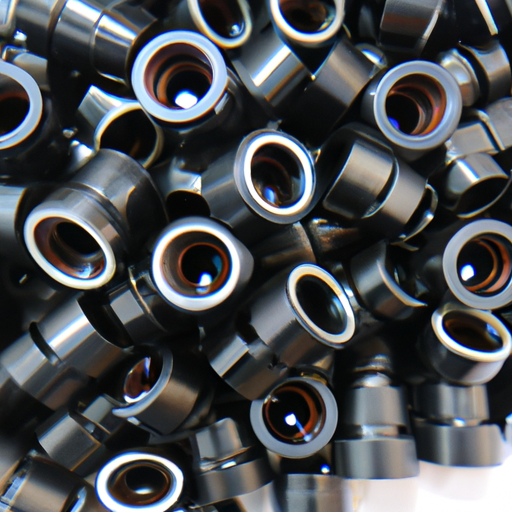
1. Design and Engineering:
The production process of SUB connectors begins with the design and engineering phase. This phase involves designing the connector based on the specific requirements and specifications of the application. The design process includes determining the size, shape, and configuration of the connector, as well as the materials to be used. Engineers also consider factors such as electrical performance, durability, and environmental conditions when designing SUB connectors.
2. Material Selection:
Once the design is finalized, the next step in the production process is material selection. SUB connectors are typically made from high-quality materials such as stainless steel, brass, or aluminum. These materials are chosen for their durability, conductivity, and resistance to corrosion. The selection of materials is crucial to ensure the reliability and performance of the connector in various operating conditions.
3. Manufacturing Process:
The manufacturing process of SUB connectors involves several steps, including machining, assembly, and testing. The first step in the manufacturing process is machining, where the connector components are fabricated from raw materials using precision machining techniques such as milling, turning, and drilling. This step requires high precision and accuracy to ensure the components meet the design specifications.
After machining, the connector components are assembled using specialized tools and equipment. The assembly process involves connecting the individual components, such as pins, sockets, and shells, to create the final SUB connector. This step requires skilled technicians to ensure proper alignment and connection of the components.
4. Plating and Coating:
Once the SUB connector is assembled, the next step in the production process is plating and coating. Plating is a process where a thin layer of metal is applied to the connector components to improve conductivity, corrosion resistance, and durability. Common plating materials used for SUB connectors include gold, nickel, and tin.
Coating is another important step in the production process, where a protective coating is applied to the connector to enhance its performance and longevity. Coatings such as epoxy, silicone, or polyurethane are applied to the connector to provide insulation, moisture resistance, and environmental protection.
5. Quality Control and Testing:
Quality control and testing are essential steps in the production process of SUB connectors to ensure the connectors meet the required standards and specifications. Quality control involves inspecting the connector components for defects, such as cracks, burrs, or misalignments, and ensuring they meet the design requirements.
Testing is another critical step in the production process, where the SUB connectors are subjected to various tests to evaluate their performance and reliability. Common tests conducted on SUB connectors include electrical testing, mechanical testing, and environmental testing. These tests help identify any issues or defects in the connectors and ensure they meet the required performance standards.
6. Packaging and Shipping:
Once the SUB connectors have passed quality control and testing, the final step in the production process is packaging and shipping. The connectors are carefully packaged to protect them from damage during transportation and storage. Packaging materials such as foam inserts, anti-static bags, and cardboard boxes are used to ensure the connectors are securely packaged.
After packaging, the SUB connectors are shipped to customers or distributors for use in various electronic devices and applications. Proper handling and storage of the connectors are essential to maintain their quality and performance until they are installed in the final product.
In conclusion, the production process of SUB connectors involves several steps, including design and engineering, material selection, manufacturing, plating and coating, quality control and testing, and packaging and shipping. Each step in the production process is crucial to ensure the connectors meet the required standards and specifications for performance and reliability. By following a systematic and rigorous production process, manufacturers can produce high-quality SUB connectors that meet the demands of modern electronic devices and applications.
The SUB connector, also known as a Subminiature connector, is a type of electrical connector commonly used in various electronic devices and applications. These connectors are smaller in size compared to standard connectors, making them ideal for compact and space-constrained devices. The production process of SUB connectors involves several steps to ensure high quality and reliability. In this article, we will discuss the mainstream production process of SUB connectors in detail.
enter;margin:5px 0;'>
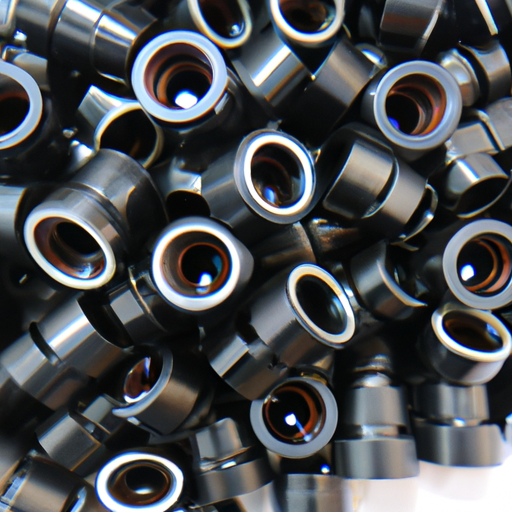
1. Design and Engineering:
The production process of SUB connectors begins with the design and engineering phase. This phase involves designing the connector based on the specific requirements and specifications of the application. The design process includes determining the size, shape, and configuration of the connector, as well as the materials to be used. Engineers also consider factors such as electrical performance, durability, and environmental conditions when designing SUB connectors.
2. Material Selection:
Once the design is finalized, the next step in the production process is material selection. SUB connectors are typically made from high-quality materials such as stainless steel, brass, or aluminum. These materials are chosen for their durability, conductivity, and resistance to corrosion. The selection of materials is crucial to ensure the reliability and performance of the connector in various operating conditions.
3. Manufacturing Process:
The manufacturing process of SUB connectors involves several steps, including machining, assembly, and testing. The first step in the manufacturing process is machining, where the connector components are fabricated from raw materials using precision machining techniques such as milling, turning, and drilling. This step requires high precision and accuracy to ensure the components meet the design specifications.
After machining, the connector components are assembled using specialized tools and equipment. The assembly process involves connecting the individual components, such as pins, sockets, and shells, to create the final SUB connector. This step requires skilled technicians to ensure proper alignment and connection of the components.
4. Plating and Coating:
Once the SUB connector is assembled, the next step in the production process is plating and coating. Plating is a process where a thin layer of metal is applied to the connector components to improve conductivity, corrosion resistance, and durability. Common plating materials used for SUB connectors include gold, nickel, and tin.
Coating is another important step in the production process, where a protective coating is applied to the connector to enhance its performance and longevity. Coatings such as epoxy, silicone, or polyurethane are applied to the connector to provide insulation, moisture resistance, and environmental protection.
5. Quality Control and Testing:
Quality control and testing are essential steps in the production process of SUB connectors to ensure the connectors meet the required standards and specifications. Quality control involves inspecting the connector components for defects, such as cracks, burrs, or misalignments, and ensuring they meet the design requirements.
Testing is another critical step in the production process, where the SUB connectors are subjected to various tests to evaluate their performance and reliability. Common tests conducted on SUB connectors include electrical testing, mechanical testing, and environmental testing. These tests help identify any issues or defects in the connectors and ensure they meet the required performance standards.
6. Packaging and Shipping:
Once the SUB connectors have passed quality control and testing, the final step in the production process is packaging and shipping. The connectors are carefully packaged to protect them from damage during transportation and storage. Packaging materials such as foam inserts, anti-static bags, and cardboard boxes are used to ensure the connectors are securely packaged.
After packaging, the SUB connectors are shipped to customers or distributors for use in various electronic devices and applications. Proper handling and storage of the connectors are essential to maintain their quality and performance until they are installed in the final product.
In conclusion, the production process of SUB connectors involves several steps, including design and engineering, material selection, manufacturing, plating and coating, quality control and testing, and packaging and shipping. Each step in the production process is crucial to ensure the connectors meet the required standards and specifications for performance and reliability. By following a systematic and rigorous production process, manufacturers can produce high-quality SUB connectors that meet the demands of modern electronic devices and applications.